It took over 5,000 hours of old-world skills to hand-craft this masterful pipe organ
For over a year, videographer Mike Tripp followed along as craftsmen built Opus 71 for a behind the scenes look at the art of building pipe organs with Taylor & Boody Organ Builders in Staunton, Virginia.
MIKE TRIPP’S VIDEO FOLLOWS CRAFTSMEN AT TAYLOR & BOODY FOR OVER A YEAR AS THEY BUILD A GIANT MUSICAL INSTRUMENT.
by Mike Tripp / The News Leader
To see nearly 5,000 hours and over a year’s worth of work condensed into five minutes, watch the video above.
THERE WAS FIRE AND SMOKE, the smell of burning, and the screeching sound of a hot conical burning iron searing the holes in a plank of white oak a shiny black. It was a sunny December afternoon. From the top of a hill surrounded by bare trees, the sounds and smell of an odd ritual drifted down.
It was rack-burning day.
Nobody witnessing the scene would have guessed that what was happening on the loading dock of an old brick schoolhouse-turned-workshop was the creation of a key piece of structural support for what would become a magnificent pipe organ.
But inside, almost a year of work by over a dozen craftsmen had led to this moment. The raw and elemental nature of the rack burning contrasted with the fine-tuning of practically every piece that would get put together into a complex and remarkable musical instrument, including over 300 hand-crafted metal pipes which would find their proper place in the carefully measured and bored racks within the organ’s case.
Go inside the workshop
YOU COULD SAY the work actually started decades ago, when John Boody, as an 11-year-old at choir camp in New Hampshire, helped take apart the local church’s organ to clear out the acorns that squirrels had stored there, and became entranced by the mechanics behind the music.
You could say the work really started overseas in Germany, where a young George Taylor apprenticed himself to a famous pipe organ builder, learning the trade from the ground up.
You could say the work started in Ohio in 1970 when the two met and built their first pipe organ in a garage.
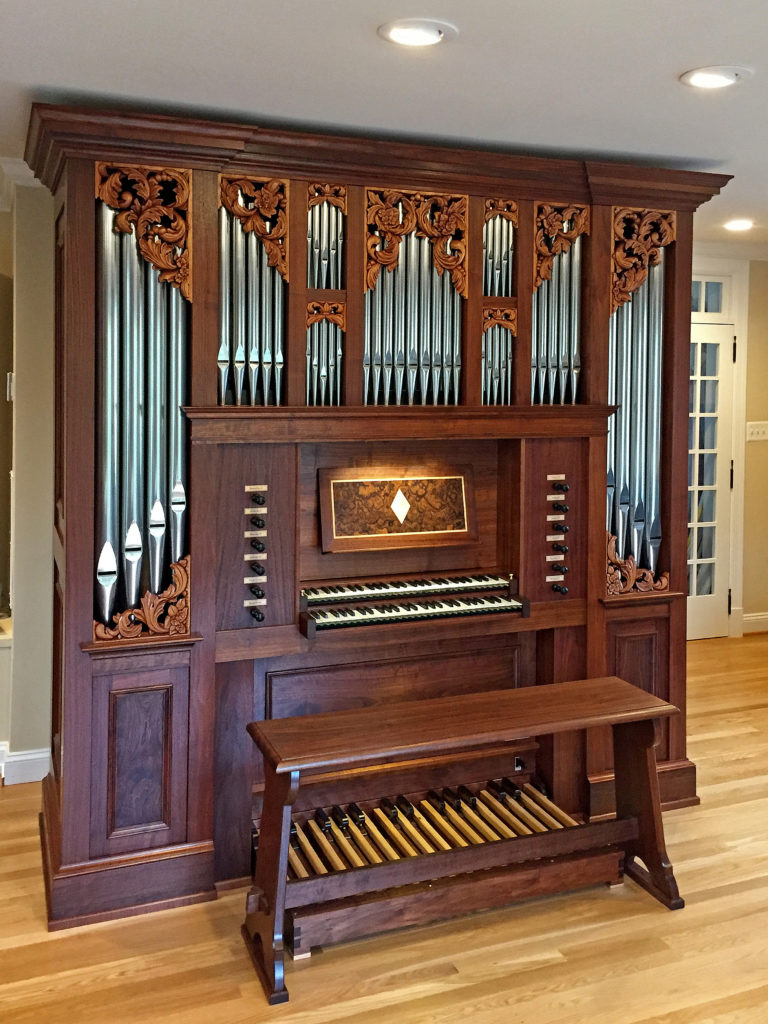
But this particular organ — Opus 71, which literally means “work number 71” — really started in the mind of Giles Cooke, an organist who decided in 2015 that his new music room had just enough space, even with the low 8-foot ceilings, for a custom-built organ.
And he turned to Taylor & Boody to design and build it.
News Leader videographer Mike Tripp spent over a year visiting the Taylor & Boody workshop on the outskirts of Staunton as over a dozen skilled workers did everything from designing the organ to fit in Cooke’s room to melting lead and tin blocks and shaping the pipes, constructing the wooden pipes and the case, “voicing” each pipe before installation, and marrying the combination of old-world skills like wood carving and new-world electrical craft into an engineering feat taking over 4,500 hours.
Later, after an open-house at which Opus 71 was played for its new owner and the public, it was taken down for travel and driven to Silver Spring, Maryland, where it was installed in its new permanent home between February 20-25, 2017.
Hear their stories
See nearly five thousand hours of work in less than five minutes! Don’t miss the video at the top of the story.
Recent Comments